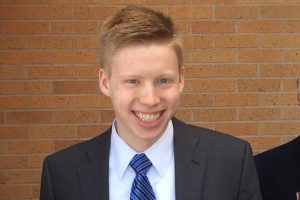
Clayton’s role as a Boeing systems engineer working directly with the aircraft mechanics has given him what he calls a “front-row seat” to aircraft production and its challenges.
“My job has helped me learn a lot about what it takes to manufacture and assemble aircraft, including fuel tank requirements,” he said. “Workers need to enter fuel tanks during assembly to perform various tasks in a very confined space. These processes follow careful safety procedures, but the hazardous space constraints increase manufacturing costs, time, and risk.”
Recognizing the potential safety and ergonomic hazards confronted by workers who must enter aircraft fuel tanks, Clayton created the “Automated Aircraft Fuel Tank Access System” for his Systems Engineering capstone project.
What specific aspects of fuel tank entry does your project seek to address?
My project focused on sealing and inspecting fuel tanks during initial aircraft assembly, which are among the many tasks that require fuel tank access.
The current process requires workers to follow stringent safety guidelines and take all appropriate precautions, but even so, the task of entering a fuel tank is cumbersome, ergonomically challenging, and poses inherent risks that cannot be fully eliminated.
What was your solution? How does it do the job better than systems already in use?
My project provides a concept for how an automated system could be used to accomplish aircraft fuel tank sealing and inspections, thus minimizing the need for human entry into the fuel tanks to perform these tasks. The automated system proposes using equipment including a robotic arm, cameras, and other sensors that would both do the work of sealing the tank and then perform an inspection. The system architecture includes an automated mechanical system to apply the sealant to the tank as well as a three-dimensional scanning process to ensure that the sealant is applied in the correct locations. This system also allows the human operator to monitor the process without having to enter the fuel tank. The system is designed to maintain the same quality of the sealing process while increasing the comfort and safety for the human operator.
Tell us about how you approached this problem using systems engineering.
I began by thoroughly researching the problem to work up a comprehensive needs analysis. In turn, this led to a concept of operations (CONOPS) and the development of system requirements. Then I laid out an architecture for how the system needed to operate—what we call a “functional analysis”—and then drafted the system’s physical architecture. It was important to iterate and refine the concepts and decisions from previous steps in the process at each stage of the systems engineering process.
Why is this work important? Do you see your system being implemented in real life?
This problem is incredibly important. As engineers and product developers, it is vital that we always remember the human element in our design and manufacturing. This project is one small step to help reduce the risk posed to mechanics and technicians when performing tasks that require aircraft fuel tank entry. It also has the potential to help alleviate some of the costly elements currently required due to the manual nature of the current process.
Are you planning to continue to work on this?
At this time, I will not be further involved in this project, but I know that this is a problem area that continues to be the focus of industry interest and research. As manufacturing technology continues to improve and automation advances, it seems likely that a concept like the one presented in this project will eventually emerge to help alleviate some of the needs I have highlighted.
More importantly, I am finding that the systems engineering principles I learned through hands-on experience in this project are invaluable and benefit me daily in my current engineering role. They provide a crucial foundation for the design, development, and fielding of complex systems.