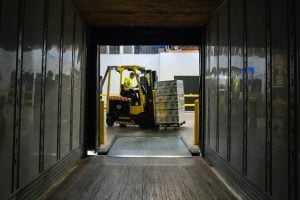
During his more than two decades as an occupational health and safety engineer at Ford Motor Company in Dearborn, Michigan, Scott Houghton was responsible for protecting his co-workers from being involved in these types of accidents by implementing forklift safety awareness programs.
For his final Systems Engineering project, Houghton—now a corporate industrial hygienist at Ford—has gone a step further, designing a system that reduces workers’ risk of being injured by one of these 9,000-pound vehicles in the first place.
“I knew that systems engineering principles could be leveraged to apply emerging technology to prevent forklift truck accidents”, said Houghton.
His ‘Safety Sentinel System’ uses tracking technology to identify potentially hazardous situations between workers and forklift trucks and to avert disaster before it happens.
Here is how it works:
Antennas in the building send a signal to a small device (a tag) worn by workers and mounted on the forklift trucks. These tags can pinpoint the location of each party with startling accuracy: within a few inches. A central computer tracks the workers’ and forklifts’ movements and predicts potential collisions when their paths intersect. When the computer detects a potentially unsafe situation is developing, it wirelessly sends a warning to both the person operating the forklift and to pedestrians walking nearby. And when the system detects imminent danger, it wirelessly activates the forklift’s brakes to prevent a collision.
“Because the system knows the location of all vehicles and pedestrians, it can also identify the least congested travel routes and send that information to a display on the forklift truck, similar to an automobile navigation system”, Houghton said.
He is quick to point out that many companies have already adopted safety measures to make forklifts more visible and use presence-sensing technologies to warn the vehicle operator when a worker is getting too close. However, Houghton’s system is an improvement, as it doesn’t rely on the responses and reflexes of the forklift operator, but instead has the capability to act autonomously to prevent potential accidents.
Though all of the technology needed to make the ‘Safety Sentinel System’ a reality exists at this time, the challenge lies in integrating all components so that they operate smoothly and reliably, according to Houghton.
“Complex software would have to be developed to implement the system”, he explained. “In a large manufacturing plant, there would be hundreds of vehicles and thousands of pedestrians to manage simultaneously in a shared space. For my proposed system, it may be more feasible to implement it first in a smaller, high-risk area such as a shipping and receiving dock, rather than an entire manufacturing plant.”
Houghton said that even if his system as designed is never implemented, the project was enormously valuable.
“It was a great demonstration of the concept that ‘perfect is the enemy of good enough,’ which is something my professors talked about”, he said, referring to the need to balance competing objectives. “A big takeaway for me is that the process was very iterative and it was OK—in fact, required—to change the requirements as you went along and learned more about the system. Though I don’t usually have a direct role in engineering projects at work like many of my fellow students do, the lessons learned from the SE program can definitely be applied to my current role, or any future job assignment.”
The Systems Engineering program at Johns Hopkins Engineering regularly highlights the design projects and in-depth thesis research of its students. We will continue to make these presentations available so that they can benefit the entire systems engineering community.